How robotic roller hemming provides quality results
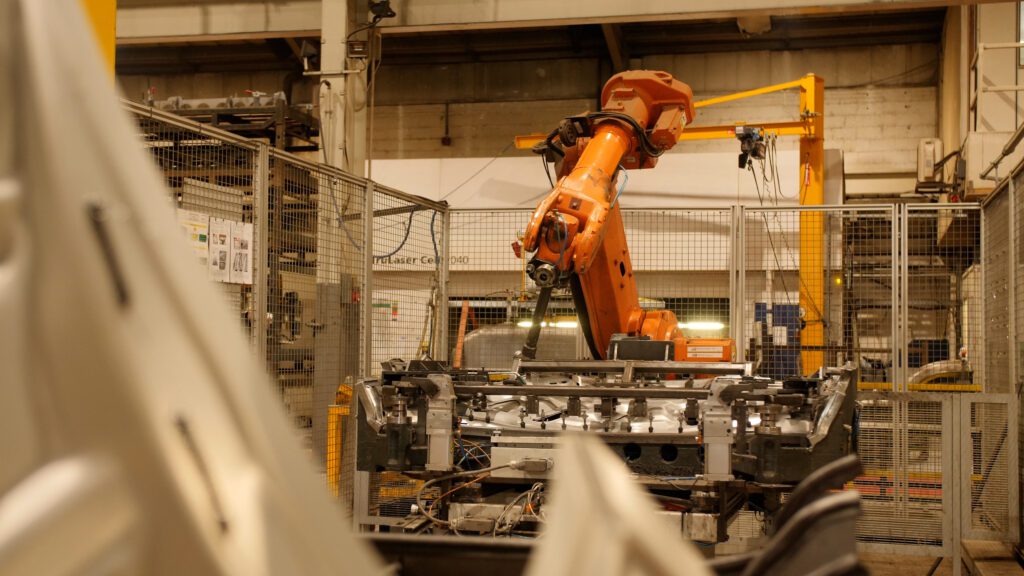
Robotic roller hemming is one of ADM’s core capabilities, offering our clients a number of advantages over other methods of hemming. Read on to find out more…
Hemming and the automotive industry
Hemming is a technique used in the automotive industry to join inner and outer closure panels together. The components can be of the same or different materials.
Hemming technology can be used to join a range of vehicle components including bonnets, doors, sun roofs and wheelhouses, aswell as special applications such as fuel lid, brand and special parts.
How does hemming work?
When two sheet metal parts are hemmed, the edge of the outer panel is folded over the edge of the inner one to create a rim. The hemmed edge will have a structural adhesive applied before folding over which seals and bonds the joint together.
Whilst it connects parts together, hemming also reinforces the edges of the part, increasing its resistance and rigidity. It also improves the final geometry and general appearance of the part.
Usually the last stage of production, hemming plays an important role in assuring the quality of the final assembly.
What types of hemming techniques are there?
There are two different hemming systems to choose from:
- Table top hemming joins components using an automatic electro-mechanical system.
- Robotic roller hemming joins components using a standard industrial robot integrated with a roller hemming head. The roll hemming is carried out incrementally, the robot guiding the hemming roller to form the rim.
Which technique is more suitable will depend on the component being hemmed and cycle time requirements. Tabletop hemming, for instance, is characterized by particularly short process times, making it particularly suitable for high-volume models with large batch sizes.
Why use robotic roller hemming?
At ADM we believe that our robotic roller hemming capabilities provide a simple and economic alternative to table-top hemming, offering many advantages for assembly production:
Flexibility:
The biggest advantage that robotized roller hemming offers is the way it can be adapted and applied in so many different ways.
For instance, the hemming robots can be programmed to hem different parts and components, meaning that they can be used on different vehicles. What’s more, they can also be programmed to perform tasks other than hemming, such as welding or gripping, making them a valuable asset to any assembly process.
The hemming rollers themselves are also incredibly versatile and can be designed according to the part being hemmed or any other particular specification required.
Efficiency:
The use of programmable robots also means that the hemming process is as efficient as possible – indeed, the hemming roller and the robot are so closely synchronised that it is possible to significantly reduce production time.
Similarly, roller hemming tool costs can be considerably lower than those of table-top hemming, requiring lower investment and maintenance costs.
Precision:
Most importantly, our robotic roller hemming delivers in terms of quality. As mentioned earlier, as the final step in the production process, hemming as a big impact on the final quality of the product.
Luckily, the robotic roller hemming process can executed to the highest levels of precision: for example, we are able to control the hemming pressure along the entire length of rim, reducing the effects of angle and length variations.
As a result, our robots can deliver consistently high quality outcomes both in terms of the geometry and the appearance of the final parts.
Robotic roller hemming at ADM Pressings
At ADM we are committed to investing in cutting edge technology and offering the very best service to our OEM and Tier 1 clients.
We are proud to operate three roller hemmer robots at our 305,000sq ft site in Newcastle. Our robotic roller hemmers operate at three levels of reach, capacity and controller specification:
Roller Hemmer 1:
- Max Reach: 2000mm
- Max Handling Capacity: 150kg
- Controller Spec: KRC V5.2.15
Roller Hemmer 2
- Max Reach: 2550mm
- Max Handling Capacity: 235kg
- Controller Spec: S4
Roller Hemmer 3:
- Max Reach: 2550mm
- Max Handling Capacity: 235kg
- Controller Spec: IRC5
With our robots, we can demonstrate that robotic roller hemming is a simple and economic alternative to table-top hemming, offering a higher degree of flexibility and precision.
To find out more about ADM’s robotic roller hemming capabilities get in touch.