Robotic roller hemming: what is involved?
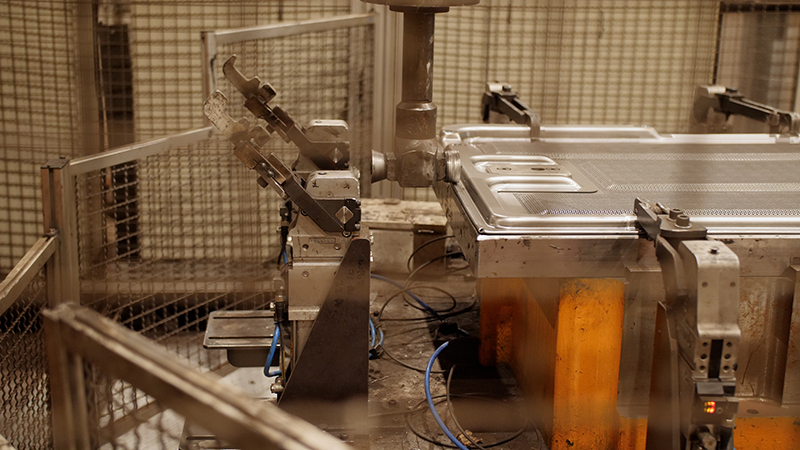
A simple and economic alternative to table-top hemming, robotic roller hemming offers flexibility with high quality results every time – but how does it work? Let’s take a look…
How it works
Robotic roller hemming joins components by guiding a hemming roller head along the outer flanges of a sheet metal component, hemming it over an inner panel which is nested in a die.
Whereas table-top hemming joins components using an automatic electro-mechanical system, robotic roller hemming is carried out incrementally, allowing greater flexibility and precision.
Applications in the automotive industry
The precision robotic roller hemming provides means that it is ideal for hemming vehicle components including:
- Doors
- Bonnets
- Wheel houses
- Sun roofs
It is also highly suited to special applications such as fuel lid, brand and special parts.
Robotic roller hemming technology
Robotic roller hemmers consist of a standard industrial robot integrated with a roller hemming head.
Robot:
The industrial robots be can be programmed to hem different parts and components, meaning that they can be used on different vehicles.
They can also be programmed to perform tasks other than hemming, such as welding or gripping, making them a valuable asset to any assembly process.
Roller hemming head:
The roller hemming head consists of a body, some guides and a number of rolls that are designed according to the geometry of the part in each case.
The hemming rollers are very versatile and can be configured to meet the specifications of the part being hemmed – the angle, for example, can be configured to 150º for closures and up to 180º for sun-roofs.
The advantages of robotic roller hemmers
Suitable for all projects
Customisable and versatile, roller hemming robots can be programmed to meet the needs of any project and required production volume.
Efficient turnaround
The hemming roller and the robot are so closely synchronised that they operate with the highest efficiency, resulting in reduced production times.
Quality output
The ability to control hemming pressure along the entire flange length means that there are fewer variations due to flange angle and length variations, delivering high quality results time and time again.
Versatility in production
As the roller hemming robots are highly versatile, they can be quickly adapted to produce different parts through program changes, making them a valuable asset to any production line.
Lower cost implications
With lower investment and maintenance costs, in-house roller hemming can be considerably cheaper than table-top hemming.
Robotic roller hemming at ADM Pressings
We operate three roller hemmer robots at our site in Newcastle. Our robotic roller hemmers operate at three levels:
- Reach: maximum of 2550mm
- Capacity: maximum of 235kg
- Controller specification: KRC V5.2.15, S4 & IRC5
If you are an OEM and Tier 1 clients in the automotive industry, our robotic roller hemming capabilities offer precision-engineered added-value solutions to your production needs.
To find out more get in touch today.