How robotic welding joins the dots
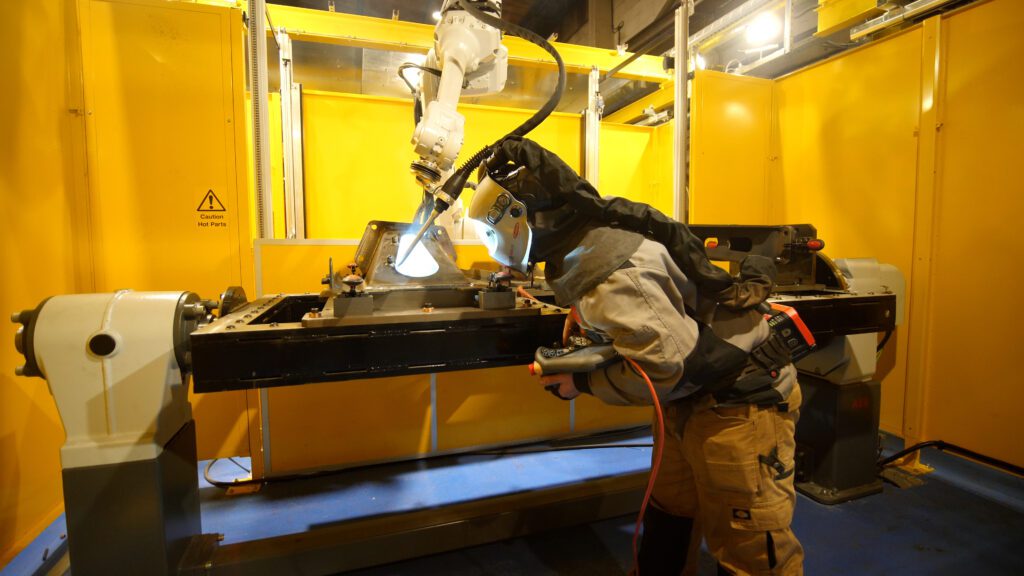
Robotic welding is one of ADM’s key capabilities, but what does it involve and why is it so popular? We take a look…
What is robotic welding?
Also known automated welding, robotic welding is the process of using mechanized programmable tools to weld and handle a part.
The robot – or cell, as it is often referred to – typically comprises of a number key components including:
- Controller
- Wire feeder
- Robotic arm
- Torch
- Wire cleaner
A human operator programmes the cell via the controller. The wire feeder then sends the filler wire to the robot as it needs it, the heat torch at the end of the arm melting metal to enable the welding process.
As it waits on the next parts to weld, the arm moves the torch to the cleaner to remove any metal splatters from the arm before they can solidify in place.
Find out more about ADM’s robotic welding capabilities
Robotic welding v manual welding: the benefits
The manufacturing and engineering industries are increasingly using robotic welding, for both resistance spot welding and arc welding, as these automated systems offer a number of advantages over human welders:
Continuous output
By their very nature, robots can work 24/7, seven days a week. Not only can they operate continuously, robot cells can also withstand a greater arc on-time and move more quickly between weld joint positions.
As a result, robots can provide substantial increases in output – up to five times faster than manual welding.
Reduced waste and lower production costs
Manual welds can often end up larger than required, wasting time and materials in the process. Robotic welders can be programmed to weld to the correct length and size required every time.
Through saving time and consumables and reducing scrap, these systems can result in cost savings, not to mention lower energy consumption and other associated costs of the project.
Consistent and repeatable results
Whereas manual welding relies on the level of skill and concentration of the welder, robotic welding can achieve precisely the same results continuously, 24 hours a day, seven days a week.
Programmed with the correct welding angle, speed and distance, robotic welders can deliver results at a consistently high standard.
Versatile production solutions
Robot cells can grip parts of any size or shape, position them on the assembly and hold them in place throughout the process.
With no tool changes required, this offers greater flexibility than manual processes, which require different jigs each production run.
Return of investment
Whilst there are initial set up costs associated with a robotic welding system, there is a quick return of investment when you consider the greater speeds, higher-quality welds and decreased waste.
What’s more, with the reduced energy costs and minimized chances of overwelding, an automated process can result in significant overall savings.
A safer workplace
Like all automated systems, robotic welding cells come with multiple safety features. For example, arc shields prevent the high-heat arc from mixing with oxygen, and enclosed areas protect operators from the temperatures and bright light.
As a result, the use of robotic welders greatly reduce the risk of on-site injuries such as electric shock, flash burns to the eyes and exposure to gases and toxic fumes.
When robots aren’t the answer
Of course, there are situations when automated systems do not meet the needs of the project:
Less flexibility
Robotic cells cannot react to unexpected situations as quickly as a human welder can. If a robotic welder needs to make a change, the operator must stop its process and reprogram it, which can increase production time.
Less suitable for smaller projects
Depending on the size of the project, the time needed to program the robotic cell may be longer than the welding process required.
Smaller projects may therefore require a human welder who can finish the task quicker
Manufacturers like ADM may therefore provide both manual and automated welding capabilities in order to meet client’s needs.
ADM: robotic welding capacity to suit every requirement
As a world-class supplier to OEM and Tier One clients, we are renowned for our technological and operational excellence.
We have invested in our robotic welding capacity and our Newcastle site has state of the art automatic and semi-automatic cells for one-off projects or production lines.
Semiautomatic robotic welding systems:
Controlled by experienced ADM engineers, who will program the robot to perform a simple task, our semiautomatic welding cells are ideal for smaller-scale projects
Automatic robotic welding systems:
Our fully automatic robotic cells can be given a series of commands, involving the machine in the entire line function.
A more intricate robotic welding system, they are particularly well suited to the automotive industry, where uninterrupted production flow is required.
To find out how our robotic welding systems could be used in the manufacture of your product, get in touch today.